Tech Blog
While there are many sensing technologies to measure linear (straight-line) position or displacement (as opposed to micro position sensing such as strain gage, capacitive, or laser technologies) most are not suitable for use in environments known to be “Hazardous Locations”, commonly referred to as “Hazlocs”. So, what are “hazloc” areas? The answer is both simple and straight-forward, but with several nuances.
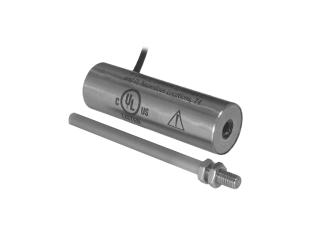
For analog sensor data transmission, a 4-20 mA current loop is a very common method to convey the sensor data acquired.
Periodically the need arises to be able to measure the primary impedance of an LVDT to ensure that it will work with a particular version of signal conditioning electronics. Typical LVDT signal conditioner systems are built to work with a primary impedance of 200 Ohms or higher, but some systems cannot supply enough excitation power to operate an ordinary industrial LVDT.
Most analog output sensors have general specifications such as linearity (or non-linearity), repeatability, and resolution, as well as environmental specifications like operating temperature or shock and vibration, and dynamic specifications like response or bandwidth. All of these specifications represent limits of error or sources of uncertainty related to the sensor's output compared to its input. Many of these terms are fairly easy to understand by their wording alone, but linearity error or non-linearity is not in that category.
Alliance Sensors Group’s PG Series LVDTs Prove Their Durability Once Again
The PG series of heavy duty LVDT position sensors from Alliance Sensors Group have become the defacto standard of the power gen industry for measuring steam valve position on power plant turbines, having demonstrated outstanding performance, reliability, and durability over many years of operation.
These LVDTs ’ robust construction is clearly illustrated by the following pictures from a power plant in which the failure of the anti-rotation mechanism on the shaft of the hydraulic actuator operating a modulating steam valve while the turbine was operating resulted in extreme misalignment of the LVDTs’ extension rods, as shown in Figure 1 below.