Blog
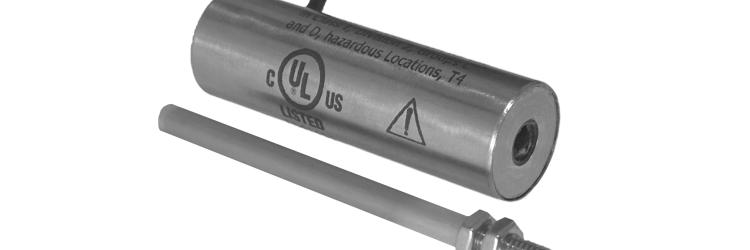
While there are many sensing technologies to measure linear (straight-line) position or displacement (as opposed to micro position sensing such as strain gage, capacitive, or laser technologies) most are not suitable for use in environments known to be “Hazardous Locations”, commonly referred to as “Hazlocs”. So, what are “hazloc” areas? The answer is both simple and straight-forward, but with several nuances.
By definition, a Hazardous Location is an area where there is a potential for an explosion or fire due to the presence of flammable gases, flammable liquid vapors, or combustible dust particles. Examples of classic hazlocs include: oil or gas fields and refineries, chemical processing plants, grain or saw mills, and coal mines.
To ensure a safe environment for personnel and operation of equipment, and to avoid potentially catastrophic accidents, various government and standards-setting organizations, both in the USA and internationally, have cooperated in the development of classifications for hazardous locations.
In the USA, these hazloc classifications are laid out in Sections 500 and 505 of the National Electrical Code (NEC), published by the National Fire Protection Association (NFPA), while mine hazlocs are in the jurisdiction of OSHA. The International Electrotechnical Commission (IEC) has developed the hazloc classifications used by practically all the rest of the countries in the world. Some countries have their own national standards organizations that utilize the IEC hazloc classifications but accept most certifications of products meeting the protocols for operation in IEC hazloc classifications.
The NEC 500 divides up hazloc classifications into hazard Classes, Divisions, and Groups. NEC 505 and IEC divide hazloc classifications by combining the NEC hazard Classes and Divisions into Zones and then Groups. Both systems use either the likelihood or the duration of a given hazard as a major distinguishing point. Probability or duration choices are differences between these two systems, but both intend to achieve the same safety goals within a hazardous location.
The NEC 500 Divisions are based on whether a hazard exists during normal or abnormal operations and for how long the hazard will be present, whereas the NEC 505/IEC Zones are based on how often or how long a hazardous situation exists. NEC Classes, Divisions, and Groups and the IEC Zones and Groups are compared in Table 1. Suffice it to say that NEC Class I applies to any area where flammable gases or flammable liquid vapors can be present. NEC Class II applies to areas with combustible dust such as grain, flour, sawdust, and coal dust.
NEC Class I, Div 1 overlaps IEC Zones 0 and I for the most hazardous locations with the hazard being continuously or frequently present. NEC Class I, Div 2 matches IEC Zone II, and both cover infrequent hazlocs, based on the rarity of exposure, usually under abnormal conditions. NEC Groups are shown in Table 1, along with the comparable IEC Groups. Groups are based on the flammability ratings or ignition temperatures of the hazardous material. Class I approval also applies to Class II and Class III hazlocs. Materials and methods of construction determine how and where a hazloc-approved device can be used, and whether any ancillary equipment such as a hazloc safety barrier is required for proper installation.
The necessary testing to certify conformance with these standards for various products to be safely utilized in hazlocs is done by Nationally Recognized Testing Laboratories, aka NRTLS. In the USA, all NRTLS are certified by the US Dept. of Labor’s Occupational Health and Safety Administration (OSHA). Some well known NRTLS are: UL (UL Solutions), FM (FM Approvals), ETL (Intertek), CSA, and TÜV. Not all NRTLS safety-test hazloc devices; some test safety of packaging, automobiles, pressure vessels, etc.
Among the myriad hazardous locations, those comprising NEC Class I, Div 2, Groups C and D, and IEC Zone II, Groups A and B, are the ones most often found requiring linear position sensing. Some typical applications include standby electric power turbines fueled by natural gas, oil field and platform pumps and other machinery in the vicinity of well heads, tank farms with dispensing or relief valve position sensing, and safety and / or fire suppression systems in chemical processing plants and oil refineries.
The ASG LZ-19 series LVIT (Linear Variable Inductance Transducer), has full scale ranges from 0.1 inch (2.5 mm) to 30 inches (750 mm). It is a 24-Volt DC input device with one of several DC voltage outputs, or a 4-20 mA DC, 3-wire sourcing current loop output that can drive a total loop load of up to 850 Ohms, all without requiring a hazloc barrier or isolator. As noted above, the LZ-19 UL/CUL hazloc-approved LZ-19 LVIT linear position sensor series is sharply focused towards the applications and ranges for a contactless, inductive linear position sensor with self-contained electronics.
For detailed product information on the ASG LZ-19 UL/CUL-approved linear position sensor for hazlocs, please consult the ASG product page: https://alliancesensors.com/product/hazardous-location-linear-position-sensor-lvit-lz-19-ul?v=undefined